MDPF利活用事例 Vol.5
MIntを活用 - クリープ寿命低下を極力抑える溶接条件の考案
出村 雅彦
NIMS
技術開発・共用部門
部門長
プロフィール
※この利活用事例は、2024年11月5日に開催した第4回 技術開発・共用部門オープンセミナー ~MDPF利活用事例の紹介 [MInt]~(題目:AIと専門家のコラボで耐熱材料を強くする:AIの奇抜な「手」から納得の熱処理法を考案(MInt事例紹介2)講師:出村 雅彦氏)を基に作成したものです。
ポイント
- MIntによる溶接継手のクリープ寿命予測ワークフロー構築
- AIを活用した逆問題解析による溶接条件の最適化
- クリープ寿命を向上させるためのHAZ形状因子の提案
背景と目的
火力発電所などで使用される高温部材は高温高圧下での運転によってクリープ現象による損傷が蓄積します。特に、溶接した付近で損傷の蓄積が早いことが知られており、部材全体の寿命を溶接部が支配します。溶接による寿命低下を軽減できる溶接条件が見つかれば部材全体の寿命を上げることができると期待されるものの、これまでこのような観点で溶接条件を最適化することは試みられてきませんでした。クリープ試験は長時間に及ぶため、実験による試行錯誤が難しかったためです。本研究では、統合型材料開発システムMIntを活用し、2.25Cr-1Mo鋼という耐熱鋼の溶接継手を対象に、クリープ寿命を計算で予測するワークフローを構築しました。さらに、AIを用いた逆問題解析により、クリープ寿命をできるだけ低下させない最適な溶接条件を探索しました。
本研究の概要
溶接継手のクリープ寿命を予測するワークフローを作りました。熱伝導計算で熱影響部(HAZ)を特定し、母材、熱影響部、溶金部からなる有限要素モデルを構築し、クリープ損傷解析を実施しました。これにより、溶接条件からクリープ寿命を予測できるようになりました。このワークフローは、既存の研究実績を基にモジュールを統合したものです。(図1)
逆問題として、溶接によるクリープ寿命をできるかぎり低下させない溶接条件を探索しました。例えば、3層の突き合わせ溶接の場合、各層の熱量や溶接速度などのパラメータを7水準に設定すると、570万通りの条件数が考えられます。(図2)
すべての条件に対してワークフローによる予測を実行することは現実的ではありませんので、いくつかの計算結果からAIによる代理モデルを構築して、これを用いてスクリーニングすることにしました。代理モデルの構築では、溶接条件からクリープ寿命を直接結びつけるのではなく、間に、溶接熱影響部(Heat Affected Zone, HAZ)の形状を挟むという工夫をしています。具体的には、HAZの幾何学的な特徴を表す形状因子(平均幅、最大幅、界面長さなど)を専門家が考案し、溶接条件からHAZ形状因子を、HAZ形状因子からクリープ寿命を推定する2つの代理モデルをタンデム型に連結しています。こうすることで2つの利点が考えられます。一つは、溶接方法が変わっても代理モデルを再利用できることです。HAZ形状因子からクリープ寿命を推定する代理モデルは溶接方法とは独立に構築されているので、溶接が例えば4層になっても5層になっても作り直す必要はありません。(図3)
代理モデルをタンデム化するもう一つの利点は、一部を線形回帰モデルで表現できる可能性があるということです。線形回帰モデルは入力変数が目的変数に及ぼす影響を回帰係数の符号や大小で直感的に捉えることができ、現場でも使いやすいと想定されます。実際、我々はHAZ形状因子を適切に設定することで、クリープ寿命を線形回帰で表現することに成功しています。モデル選択技術を活用した結果、7つのHAZ形状因子のうち特に最大幅、自由端幅、界面長の3因子が重要であること、クリープ寿命の増加のためには、幅が狭く、荷重方向により起立した形状が有利であることがわかりました。(図4)
AI駆動の新しいタンデム型最適化手法により、初期条件49計算で見出した580時間というクリープ寿命を650時間まで延ばす溶接条件を発見できました。この条件を見出すまでに必要だった計算はわずか69回。570万通りという広大な空間の探索方法として、優れた最適化手法であったと言えます。溶接条件というプロセスとHAZ形状因子という構造、そしてクリープ寿命という性能を結びつけることで、プロセス制約のもとでの最適化問題を解くことができました。プロセス制約なしで性能から構造を最適化しようとすると、現実ではあり得ない、自明な解が得られてしまいます。例えば、本件ですと、最大幅がゼロのHAZがクリープ寿命を最も低下させないということになります。HAZの最大幅がゼロとは熱影響部がないということです。これを達成しようとすると、溶接を「しない」ことくらいしかやれることはありません。溶接を行うという制約の中で現実的な解を求めるには、構造と性能の関係だけでは不十分で、プロセスまでを考慮した順方向のワークフローを構築して最適化問題を解く必要があります。これがマテリアルズインテグレーション(シミュレーションの統合化)の意味といえます。(図5)
今後の展開
今回のクリープ寿命をターゲットとした溶接継手の最適化は計算機上で実施しました。本手法の有効性を実証するために、実際に提案された条件で溶接継手を作成し、クリープ試験によって、寿命が延びることを確認する必要があります。その結果をフィードバックすることで、順方向の計算ワークフローの精緻化も期待できます。
さらに、マテリアルズインテグレーションをベースとした逆問題デザインをさまざまな分野に広げていくことで、研究開発のサイクルの短縮が期待できます。プロセスから構造、特性、性能間の相関を一気通貫で評価し、AI最適化により、現実的な最適解を導き出すという方法論は、今後、ますます重要性が増すと考えます。
参考論文
Abe, D., Torigata, K., Izuno, H., & Demura, M. (2024)
"Study of analysis method to predict creep life of 2.25Cr-1Mo steel from welding conditions" Welding in the World, 68(5), 1297-1311.
https://rdcu.be/d0GYA
Izuno, H., Demura, M., Yamazaki, M., Minamoto, S., Sakurai, J., Nagata, K., Mototake, Y., Abe, D., & Torigata, K. (2024)
"Search for high-creep-strength welding conditions considering HAZ shape factors for 2 1/4Cr-1Mo steel" Welding in the World, 68(5), 1313-1332.
https://rdcu.be/d0GZW
Demura, M. (2024)
"Challenges in Materials Integration" ISIJ International, 64(3), 503-512.
https://www.jstage.jst.go.jp/article/isijinternational/64/3/64_ISIJINT-2023-399/_article
Demura, M. (2023)
"Challenges in Materials Integration" Tetsu-to-Hagane, 109(6), 490-500.
https://www.jstage.jst.go.jp/article/tetsutohagane/109/6/109_TETSU-2022-122/_html/-char/en
本事例で使われたDICEサービス
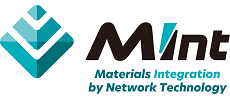
https://dice.nims.go.jp/services/MInt/
セミナーアーカイブ動画
第4回 技術開発・共用部門オープンセミナー動画
(講師:出村 雅彦氏)
本件に関する問合わせ先
国立研究開発法人物質・材料研究機構
技術開発・共用部門 材料データプラットフォーム(MDPF)運営室
Email: mdpf-pr=ml.nims.go.jp ([ = ] を [ @ ] にしてください)